気体の漏れ対策
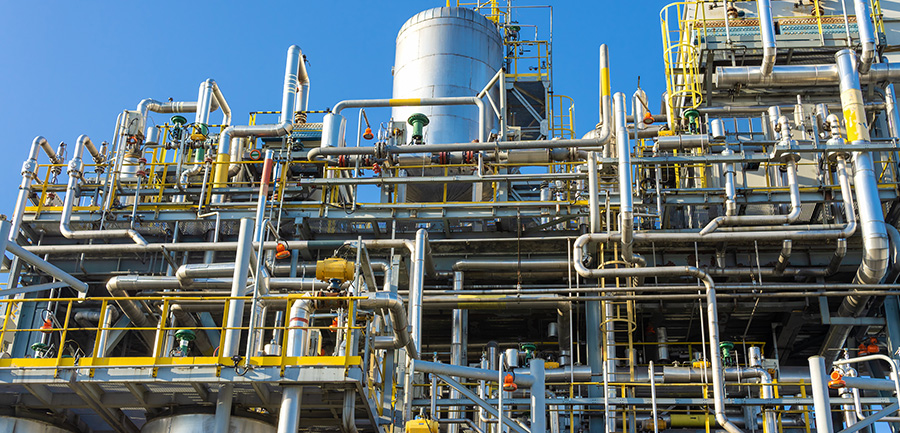
気体の漏れ対策をする理由
生産現場にはさまざまな保守・点検業務が存在しますが、エア(圧縮空気)漏れが放置されるケースが多く見受けられます。エア外の圧縮気体、特に単価が高いガスやプロセス気体とは区別して管理されることが多いと思われますが、エア自体は単価が低く危険性もないという認識から、多少の漏れはあまり気にとめられないというのが実情でしょう。
ところがエア漏れを放置してしまうと、他の希少ガスやプロセス気体が漏れ出ていても気付けない環境ができてしまいます。また、エア圧力低下による機械の突発停止、工場の安定操業を揺るがす問題となるケースもあります。
実態としてエア漏れが軽視・放置される背景として人手不足や優先度の低さがあげられるでしょう。
昨今、エアを生み出すコンプレッサーの電気代高騰、希少ガス体の単価上昇が生産コスト上昇に影響しています。こうした生産コストを抑えるために、日常的な漏れの点検、対策を実施する優先度が上がってきているのではないでしょうか。また、カーボンニュートラルの観点からもコンプレッサー負荷を軽減(=消費電力の削減)する機運が高まっています。
気体の漏れをみつけるには
漏れ量の概算値は、流量計が設置されていればその計測値を用いて、使用しているエア・ガスの総量を設備稼働時と非稼働時の値を比較すれば求めることができます。日常点検では、普段使用する頻度が高い(使用量が多い)ところや、配管接続箇所が多いエリアを重点的に確認することを推奨します。具体的な対象箇所は、開閉を頻繁に行うバルブ、稼働部のチューブやヘッダーの取り出し口等です。それらに加えて、いつもと異なる音が発生しているエリアを重点的に確認する必要があります。
確認方法・手段は、石鹸水による検査が一般的ですが、近年では超音波を用いたリーク検査器を使用する方法があります。超音波を用いたリーク検査器は初期投資はかかりますが、気体の種類を問わず手早く漏れをチェックすることが可能です。
ただし、機器の扱いが難しく、漏れを見逃してしまう場合もありますので、十分にトレーニングを積んで使用するなど活用には注意が必要です。
気体の漏れを予防するには
配管やバルブ、アクチュエータの劣化を防ぐこと自体が気体漏れの予防になります。
例えば、圧縮空気系統の場合は使用するエア内の水気を取り、クリーンエアを使用することで部品の延命につながります。逆に、同じ圧縮空気でも駆動系のエアは潤滑能力が求められますので、ルブリケータが適切に作動しているかどうか確認し潤滑能力を維持することがシール類を延命させ、漏れを抑制することにつながります。
また、使用しない配管系統は、縁切り・遮断してしまうことを推奨します。遮断されずに圧がかかっている配管系統では、使用していない範囲は点検の対象外とされてしまうことがあり、漏れが発見されない事態が生じやすいからです。
さらに、気体を輸送するためのホース、チューブの取り回しを考慮することも有効な手段となります。熱影響が懸念される場所では、熱によって傷みやすい樹脂製のホースやチューブの使用を避けることや、無理な配管施工で許容曲げ半径を超えてしまい継手部に過度な負担がかかることがないようにするなど、漏れが発生しやすい状況を抑制することも大切です。
エアガスリーク診断(点検)サービスの活用
ここまで述べてきたように、日常点検や漏れの予防を実施していくには、どうしても多くのマンパワーが必要となります。気体の種類を問わず広範囲を手早く点検できる超音波を用いたリーク検査器は、点検ツールとして有効ですが、導入に大きなコストがかかったり使いこなしに技量が必要となったりすることがネックです。
その解決策の一つとして、超音波リーク検査器の扱いに長(た)けたプロが点検を実施し、報告をする診断(点検)サービスがあります。サービスのアウトプットは漏れ箇所の写真、場所、漏れ量等を記載した報告書であり、点検後の修理活動へ役立てることが可能な実践的な内容になっています。
超音波リーク検査器を用いる診断員は、技量認定ライセンスを受けたプロであるため、機器を購入して自社で点検されている事業所でも新たな漏れを発見できる可能性があります。そのため、自社で実施する日常点検に外部の診断サービスをプラスして、日常点検では見逃しがちな漏れ箇所をカバーし健全性を保つ方法を採用されている事業所も増えてきています。
省エネ活動と工場健全性維持を気体の漏れ対策からスタートしてみましょう。