オペレーターによる振動管理で突発事故ゼロを実現 続編
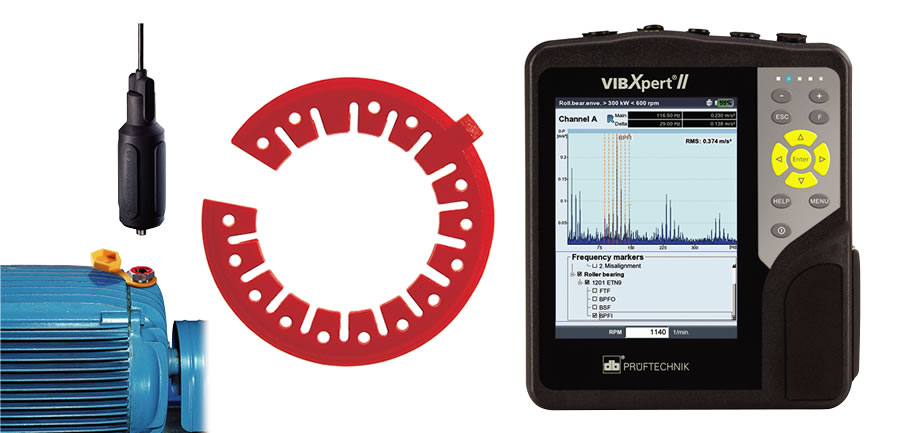
ポータブル振動計とビブコードシステム活用事例
回転機の振動を測定・管理することで成果を挙げられた事例を「オペレーターによる振動管理で突発故障ゼロを実現」でご紹介しました。 今回はこのN社様について、その後の取り組みをご紹介します。
N社様では管理するプラントと設備数を年々増やしながら、着々と成果を挙げておられ、2001年から開始したポータブル振動計とビブコードシステムによる振動管理で、
- 6年間ベアリングの突発故障による設備停止ゼロ
- トータル3.4億円の生産機会損失防止
を実現されました。
ビブコードシステムによる振動管理の全プラント展開
現在、N社様における管理対象のプラント・設備は、15プラント・620台にもなります。実にプラントの94%、設備の25%をカバーし、しかもベアリングの故障に起因する突発の設備停止事故ゼロは6年間続いています。
設置プラント数及び総台数と管理台数の推移
ポータブル振動計とビブコードシステムによる振動管理のカバー率
全工場突発件数及び内訳の推移
故障ゼロが実現すると、補修費用が発生しないので成果を金額で表現することが難しくなります。そのため、異常を発見できずに故障が生じた際に被るであろう損失額、つまり生産機会損失額を求めて、効果金額とされました。その効果金額は累計で3億4千万円になるということです。
管理手法の転換と意識の変革
また、振動管理の役割も少し変わってきました。
当初は21件と多発していた、あるプラントの突発故障の防止を最大の目的とし、製造オペレーターの技術向上、保全費削減も期待されて始まった振動管理ですが、その効果が認められると全プラントへ対象エリアが展開されました。
そして、管理を行うのは保全を担当する施設グループだけというのではなく、 製造、生産管理、更に協力会社が連携を取り合う製造部設備保全システムへと発展しました。
その流れは次のようになっています。
- 日常保全チェックシートで設備の点検を行う。異常があれば生産管理あるいは施設グループに連絡する。
- 製造部門
- バイブロチップによる振動測定を行う。万が一異常があると、異常機器連絡表を発行する。
- 生産管理グループ
- 連絡表に基づき点検修理を行い、かかった修理費を報告する。
- 施設グループ、協力会社
- 部品交換や欠陥の是正が行われた後、処置が適切に行われたことを確認するため、振動計による品質チェックを実施する。万が一、振動値に改善が見られない場合は関係部門に再是正の必要を報告する。
- 生産管理グループ
このようにメンテナンス品質のチェックが行われるようになったことで、協力会社の担当者の意識も変わったとのことです。そして、修理に要した費用も関係部門に報告されるようになったことから、コスト意識が高くなりました。
これまでの壊れれば修理すればいいという、修理対応型のメンテナンスを転換し、信頼性向上により結果としてコストが抑えられるプロアクティブなメンテナンスの方向へ、という動きにも発展しつつあるとのことです。