振動計の種類による人的誤差の比較実験
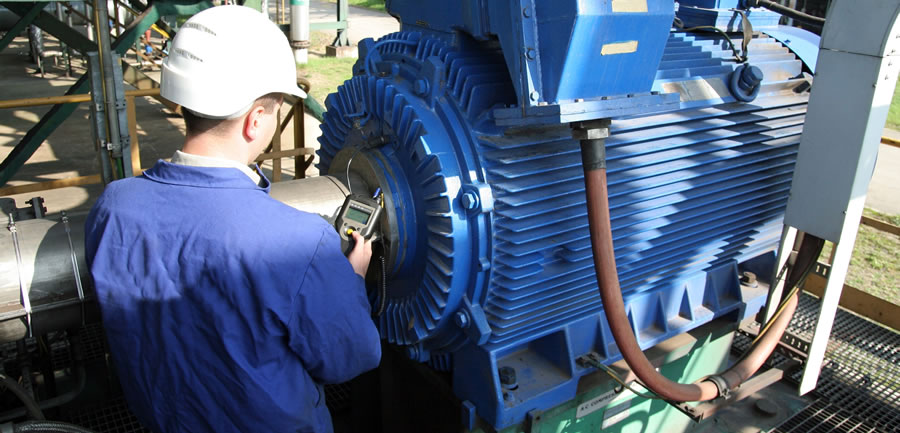
コンディション・モニタリング 正確なデータ収集の重要性
世界的な経済不況に対処するため、製造業各社は生産拠点を集約化し、設備稼働率を高めることで生産性アップによるコストダウンを強化されています。その結果、突発故障と生産機会損失を防ぐ方策としてコンディションモニタリングの重要性がますます高まっています。
今や振動計を持たない工場はおそらく無いと思われますが、最重要設備以外の一般的な設備でも、定期的な振動測定とデータのトレンド管理を行い、そのデータを突発故障防止やメンテナンス情報として活用している工場は、極めて少ないのが実情です。
振動計の用途として、パトロールで異音に気づいたオペレーターの連絡を受けて振動を測定・確認するため、ということをよく聞きます。
しかし、この使い方では現在の振動の大きさを知ることはできても、正常運転時の振動と比較できないため、生産を止めてまで修理を行うべきか、そのまま次の停止機会まで運転を続けても大丈夫なのか、緊急性の判断が困難です。
やはり振動測定データを有効に使うには、日頃から定期振動測定とトレンド管理を実践しておくことが必要といえます。
ユーザー調査結果に見る振動測定管理が実践できない理由
回転機械のメンテナンスに振動測定管理が有効だと分かっているのに実践できないのはなぜでしょうか?その答えは、当社が行ったユーザー調査の結果から伺い知ることができます。
一番の問題点として「データのバラツキ」が挙げられ、以下「データ整理に時間がかかる」「データの誤登録」と続いています。
多くの方が問題点と認識されているデータのバラツキの例として、「前回測定時には低かった振動値が突然大きくなった場合」があります。これには以下の要因が考えられます。
- 実際に損傷が発生した
- 測定条件(回転数、負荷)が前回に比べて変化した
- 測る場所を間違えた
- 測定プローブの押当て圧や押当て角度が異なっている
これらの内、3. 4.は実際の回転機の状態と無関係であり、人が測定プローブを押当てて測定することに起因しています。もしも、人的要素に起因する測定誤差を排除できる計測方法があれば、3. 4.の問題は解消できます。
実際に、ポータブル振動計でこれを解消できるのでしょうか?
3種類の振動計による比較実験
そこで、ある実験を行いました。
負荷が安定している稼動中のポンプ(110kW)をお借りして、次の3種類のプローブと3人の測定者を組み合わせ、人的要素に起因する誤差を防ぐ方法としてどれが効果的な方法か見極めようというものです。
実験は、速度と加速度の2つのモードを計測しました。3人の測定者が、3種類のプローブを使って、同時に測定を開始することで、測定者によるバラツキの影響を評価しました。
また、事前に負荷の変動による振動値の大きな変化が起こらないこと、ベアリングの状態が良好であることを確認しました。
グラフでは、バラツキの程度を判り易くするため、測定平均値に対する差を表しています。
人的測定誤差を最小限に抑えるには
ビブコードシステムで測定
実験の結果、測定者が変わっても最もバラツキのない、人的誤差を最小限に抑える測定方法は、A)のビブコードシステムであることが確認されました。
あらかじめセットしたスタッドにプローブをドッキングさせることで、測定者による押当て力や角度の差から開放され、リングコードにより測定モードが自動的に選択されることなどにより、測定値のバラツキが抑えられました。
磁石式のプローブで測定
一方、B)の磁石式では、測定者が繰り返し測定するうちに場所が少しずれたり、設置面が平坦でなかったため取付けが不安定になることがありました。
手持ちプローブで測定
そして最も不安定だったのが、C)の手持ちプローブでした。力を入れすぎるとかえって先端が滑りやすく、不安定な姿勢で測定しなければならないときは、プローブ保持と振動計のキー操作を同時に行うのがかなり困難です。このことがバラツキを誘発していると考えられます。
測定ポイントの問題以外に、実際の振動測定では、多くの測定ポイントを効率良く、できるだけ短時間で測定しなければならないため、測定箇所や測定項目の取り違えをいかに防止するかという問題もあります。
ビブコードシステムは測定箇所を自動認識し、必要な測定モードを自動的に設定するので、測定モードの取り違えというミスを防ぎ、測定作業の生産性向上による測定者の負担軽減にも繋がります。
これから振動管理を開始する、あるいはポータブル振動計で管理対象を広げることを計画されている場合に、最適なシステムと言えます。