定期メンテナンスの落とし穴
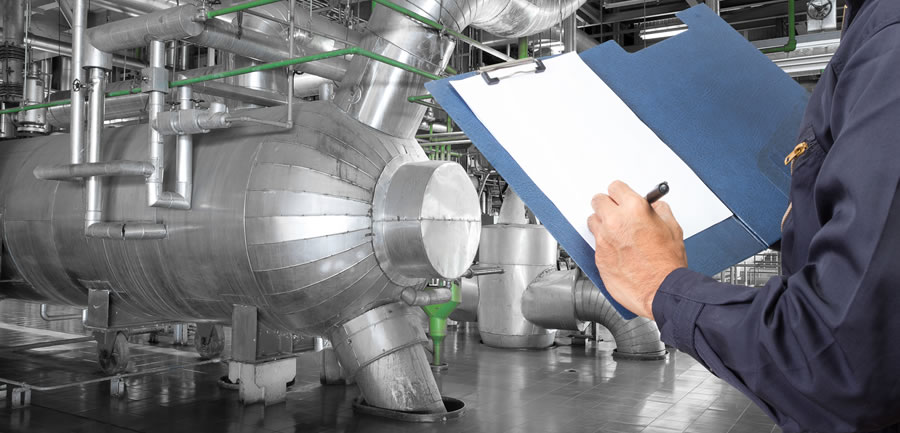
定期メンテナンスでは防げない突発故障
経済情勢が厳しくなると、保全コストの削減が必ず課題となりますが、このことによって設備運転の信頼性が損なわれ、生産に支障が出るようなことがあってはなりません。
しかし現実に、プラントの老朽化が進んだある工場では、計画された整備以外の突発的な故障が日常的に発生し、保全担当者がその対応に忙殺されています。またある工場では、半年ごとのオーバーホールをしているにもかかわらず、更にその間に数回、設備の整備を必要とする振動異常が発生しています。
このような計画外の突発故障は、緊急対応のため人件費や交換部品が割増しになったり、予定外の設備停止が生産に大きく影響して被害額が拡大します。例えば、高圧モーターの交換修理に通常の倍の費用がかかったり、設備停止による損失額が修理費用の10倍になることもあります。
これらの突発故障を、早期に発見し未然に防ぐにはどうしたら良いでしょう。定期メンテナンスよりも良い保全方法は無いのでしょうか?
従来の保全方式と特徴
従来から行われている主な保全方式として、事後保全と時間基準保全の2つがあります。
事後保全 Breakdown Maintenance
生産設備は、その運転時間に比例して構成部品が劣化するので、その性能を維持するためにオーバーホールによる整備や磨耗した部品の交換が必要です。
これを怠ると、突然機械が故障し緊急修理が必要になります。このような故障後の修理を事後保全(Breakdown Maintenance)といいますが、この対応は機械に大きなダメージを与え、長期間の生産停止や大きな事故に繋がります。
時間基準保全(定周期保全) Time Based Maintenance=TBM
そこで、一定の間隔でメンテナンスを実施して信頼性を高めようとする考え方が生まれました。これが時間基準保全あるいは定周期保全(Time based Maintenance)と呼ばれ、広く行なわれている保全方式です。
保全の間隔はこれまでの実績から設定することになり、安全のためと短めに設定されがちですが、いたずらに短くすることも得策ではありません。
保全直後のリスク「いじり壊し」
機器の使用時間と故障率の推移を表したグラフは、以下の3つの期間に区分され、その形状からバスタブ曲線としてよく知られています。
(1) 初期故障期 --- 初期:故障率は高から低に推移
(2) 偶発的故障期 --- 中期:故障率は低
(3) 磨耗故障期 --- 後期:故障率は再び低から高に推移
これは設備故障を防ぐため部品交換を行っても、すぐに故障率低下には結びつかず、(1)の初期故障の高リスクがあることを示しています。その原因は部品不良や人が部品交換を行う際のヒューマンエラー、保全現場でよく言われる「いじり壊し」などです。
故障原因を分析した結果、全故障の33%がいじり壊しなどの保守不良によるものであったとの報告もあります。
つまり、定期的にオーバーホールをすることが必ずしも、設備の信頼性向上に繋がるものではないということです。不要な整備、部品交換は保全費を押し上げる要因にもなります。
これからの保全方式「状態基準保全(CBM)」
状態基準保全 Condition Based Maintenance=CBM
このような時間基準保全の反省から、「設備が安定してその性能を発揮しているときに不要なメンテナンスを施すのではなく、必要な時に実施する」保全が求められるようになりました。
こうして生まれたのが、機械の運転中の状態、つまりコンディションをモニタリング(監視)し、ここから異常の兆候をいち早く発見して、計画的に処置するという状態基準保全(Condition Based Maintenance)です。
状態基準保全では、設備の状態に応じてメンテナンスすることで設備の信頼性を確保し、なおかつ保全コストの削減と適正化を図ることができます。