オンラインによる振動監視システム 後編 - 事例紹介
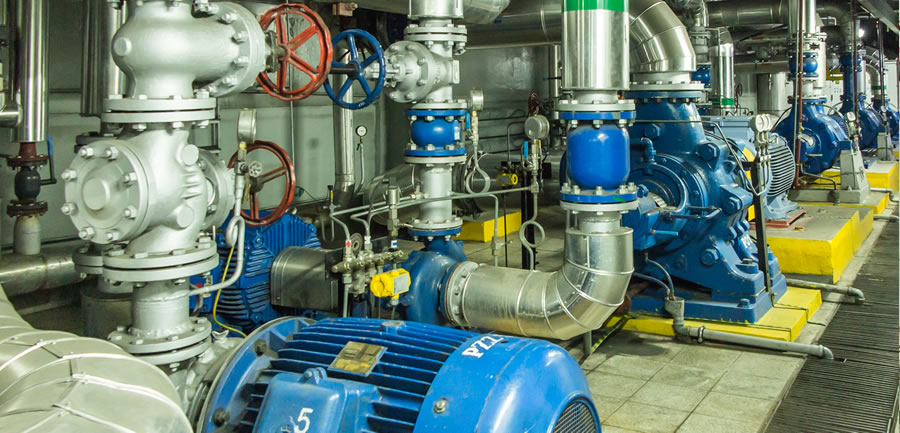
一般的な振動測定で防げない回転機の突発事故
「オンラインによる振動監視システム 前編 - システム概要」の続編として、オンライン振動測定監視システムの活用により1億円近い生産機会損失につながる突発設備停止を防ぐことができた例をご紹介します。
この工場では担当者がポータブルの振動計を使って、毎月の振動測定とトレンド管理を行い、計画的なメンテナンスを実践することで回転機械設備の突発故障防止に一定の効果を挙げていました。
ところが、突然の軸受故障、設備停止が起こり、復旧に約一週間を費やすという事態が発生しました。問題を起こしたロータリードライヤーは回転スピードが10rpmと遅く、一般的な加速度の振動測定では、正確な診断ができていなかったのです。
オンラインによる振動測定・モニタリングシステムの導入
この工場で過去20年間に発生した回転機の故障は、23%が軸受に関するものであり、特に低速回転機械における故障は軸受に集中していました 。
そこで、一週間の設備停止という大きな損失を二度と出さないよう、低速軸受の診断方法の見直しが検討され、ショックパルス計測法、AE法、低速回転専用測定法の三つの手法について比較実験がされました。
実験の結果、ショックパルス計測法とAE法が初期損傷段階から異常を検出できる手法であることが判明しました。更に詳しく検討した結果、ショックパルス計測装置は速度・加速度も測定できるのに対し、AE法は低速軸受診断だけにしか使用できないことがわかりました。」
この工場では将来的に振動測定監視を拡大していく予定でしたので、
- 多くの回転機設備をカバーできる
- 拡張性があり、少ない初期投資でも始められる
- 低コストで防爆対応できる
- オンラインでモニタリングするので少ないマンパワーで常時監視できる
といった点から、オンライン監視システムが採用されました。
そして下図はその軸受のショックパルスと加速度(5k-45kHz)の正常時と異常時のトレンドグラフです。異常時にはショックパルス、加速度共に高く、大きく変動しています。この変化によって軸受損傷が認識できるのです。事実、この軸受は内輪にフレーキングが発生していました。そして、このようなダイナミックな変動の把握はオンラインシステムならばこそと言えます。
1億円近い生産機会損失を防止
こうして2003年にロータリードライヤーへオンラインシステムを設置したのを皮切りに、現在では6プラントへ展開され、ポンプ、モーター、ブロワー、押出し機、減速機、攪拌機、冷却塔、コンプレッサーなど273測定ポイントまで拡張されています。もちろんこの中には防爆仕様の設備も含まれます。
この5年間で、進行すれば故障に至る損傷を3度早期発見・処置し、1億円近い 生産機会損失を防ぐことができました。
担当の方は、オンラインシステムをこのように展開できたキーファクターが、
- 最初に基幹部分を少ない初期投資で設置できたこと
- 製造部門と協力し毎年予算を組んで、重要度の高いプラント設備へと段階的に拡大できたこと
であると話しておられました。