上手な振動測定・管理の進め方(コンディション・モニタリング)
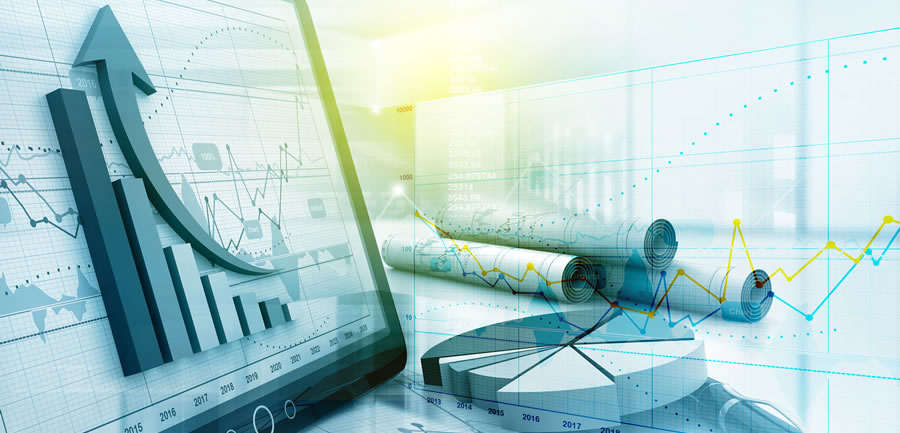
「人」に依存しない高品質メンテナンスのために
設備故障による生産停止が大きな損失に繋がることはよく知られており、生産設備の高度化により、設備メンテナンスの質が製品に与える影響の度合いは益々増しています。
反面、設備管理・メンテナンスを担当する保全部門の状況は、少人数化とベテラン技能者の退職、限られた保全予算など厳しくなる一方です。このような状況下で設備の安定稼動を達成するためには、メンテナンスの質と効率を高めることが求められています。
「ベテランの勘や経験に依存し、運転優先で早めの部品交換をするのではなく客観的なデータに基づき適切な時期に最適なメンテナンスを実施したい」
この要望を、設備の中でも特に台数の多い回転機械で実現するのが振動測定(コンディションモニタリング)です。
「自分達にもできるのか」
「継続できる?」
「本当に異常を発見できるの?」
こういった不安から、予防保全や振動測定が良いとは分かっていても、導入に踏み切れない方もおられるかもしれません。そのような方のために、振動測定・管理の具体的な始め方、運用の仕方をまとめてみました。
- 振動測定の進め方
手順 1 : 現状を調べて整理する
手順 2 : 設備の重要度、期待効果などの有効性を基に対象設備を決定
手順 3 : 判定基準を仮決定(後で必ず見直し)する
手順 4 : 振動測定頻度を設定する
手順 5 : 異常発見時のルールを決定する
手順 6 : メンテナンス業務へ測定結果を反映する
手順 7 : 成果を常に把握し公表する
手順 1 : 現状を調べて整理する
大きな突発故障や設備停止を経験すると、その対策として、「予防保全(予知保全)を即導入」「振動測定の機器を購入して直ちに運用開始」など、今までやっていなかった振動測定をいきなり始めようとしがちです。
しかし、ここで焦ってはいけません。後々導入成果を評価するために、まず現状がどうなっているのかを数字で把握しておくことが大切です。成果を具体的に数字で表し評価することは、客観性を確保すると同時に、担当者のモチベーションアップのためにも重要です。
(1) 設備のランク付け
生産への影響度合いから評価し、設備をランク付けします。その設備が故障して1時間運転停止したときの、生産への影響を金額で評価してください。また修理にどのくらいの時間がかかるかも予想します。
(2) 各設備の点検・メンテナンス情報の整理
現在各設備で実施している日常点検の項目と、メンテナンス方法(事後保全/時間基準保全)、必要メンテナンス費用、メンテナンスの実績(部位、時期等)を調べます。
(3) メンテナンスの全体像の把握
以下のデータを調査して、他との比較、成果を評価するときの客観的なベンチマーキングにします。
- 年間のメンテナンス実績の分類
(年間修理件数、計画内/計画外で実施された件数とその費用) - 頻繁に修理を行っている設備の調査
(具体的な修理箇所とその費用) - 平均故障周期(Mean Time Between Failure=MTBF)の計算
(工場全体、プラント単位、ポンプ・ファン等設備単位で算出) - 生産量に対する保全費用の比率など
手順 2 : 設備の重要度、期待効果などの有効性を基に対象設備を決定
手順 1の(1)(2)の情報を基に対象設備を選びます。その際、設定の基準は必ずしも工場全域で共通である必要はありません。どの設備に振動測定を適用することが突発停止予防に有効かという視点で選びます。
例えば、A工場では電動機容量3.7kW未満では事後保全の方が修理コストが安くなるので3.7kW以上を管理対象とし、隣のB工場では3.7kW未満でも故障頻度が高い機械を加える、などと決めていきます。
測定の対象が多ければ良いというものではありません。対象設備が多くなれば、測定にかかる工数が増大します。限られたマンパワーと費用をどのように有効に活用できるかという視点で判断します。
手順 3 : 判定基準値を仮設定(後で必ず見直し)する
速度を測定する箇所はISO、JISの判定基準を基に設定します。ベアリングのショックパルス診断では軸径と回転数から設定するメーカー判定基準を仮設定します。仮設定した基準値は、異常発見時や、部品交換・オーバーホール時には、測定値と比較して妥当性を検討し、必ず見直します。
手順 4 : 振動測定の頻度を設定する
絶対的な判定基準が確定していない限り、トレンド(傾向)を見て状態の変化を捉えることが重要です。
特に、モニタリングを始めたばかりの時期は、運転条件の変化に伴う設備の挙動変化などが掴めていません。同じ運転条件とは言いながら、実際に測定を始めてみると、人為的な測定誤差以外にも変動する要因が出てきます。異常が発生する周期もいつも同じとは限りません。異常による測定値の変化かそうでないのかを誤認しないためにも、可能な限り短いサイクルで頻繁にデータ収集=振動測定をするようにします。
手順 5 : 異常発見時のルールを決定する
「振動値が上昇している」「基準値を超えた」このような異常を発見した時、「おかしい」と感じた時、次に何をするかを事前に決めておきます。少なくとも、以下に挙げる4つのアクションは必ず行うようにルール化します。
(1) 振動値の変化をグラフで確認
急に上昇しているか、以前から上昇の傾向があったのか等確認します。
(2) 振動値の再測定
異常の疑いがある測定箇所をもう一度測定します。
(3) 再測定値を基に当面の処置決定
再測定の結果がはじめの異常値と比べて低下していれば、通常の測定頻度で経過観察をします。再測定でも高い値が測定されたら要注意扱いとします。その部位がベアリングなら給油を行い、通常測定時よりも短い周期で測定観察を継続します。その後も振動値の高い状態が改善されない場合は、メンテナンスが必要と判断し、製造部門とメンテナンス日時を調整します。
(4) 現場との情報共有
もちろん、これらの情報を設備の間近にいる現場オペレーターと共有しておくのも大事なことです。
手順 6 : メンテナンス業務へ測定結果を反映する
振動測定は異常を見つけることだけが目的ではありません。突発故障を起こさないよう、モニタリングを実施する一連の流れを通じて、設備に対する理解を深め、設備管理のスキル、メンテナンス品質、保全マネージメントの能力を高めていくことが大切です。
(1) 保全管理のスキルアップ
設備の間近に行くからには、運転音や油ゲージのチェック、温度、漏れの有無などにも気を配り、メンテナンス業務の基本や五感による状態把握のスキルも向上させていきましょう。振動計によるモニタリングを行っても、やはり設備を守る活動の土台になるのは、業務に携わる方々のスキルです。
(2) メンテナンス品質の向上
機械の更新やオーバーホール、修理後は必ず振動を測りましょう。その設備の初期状態を把握し、据付・芯出しの状態、部品交換は問題なく完了したか等が確認できます。
例えば、整備しても振動値が正常値に戻らないこともあります。整備が不十分かもしれませんし、整備した箇所以外に原因があるのかもしれません。振動測定に基づく厳しい目で見つめることで、メンテナンスの品質、意識が変わっていくはずです。
手順 7 : 成果を常に把握し公表する
振動測定の実践によりどれほどの成果が出ているのか、具体的な数値を把握し、その成果を社内で発表していきましょう。メンテナンスが生産にとってどれほど大切なものかを周知していただく良いチャンスです。
成果を判断するために、以下のような数値を見ておきます。
- 生産機会損失をどの程度防げたか
- 計画保全件数は増加したか
- 突発故障件数は減少したか
- 保全コストは低下したか
- MTBF値はどう変化したか、など
振動測定を継続するには、測定結果に沿ってメンテナンスを計画・実施し、突然の機械故障・設備停止を防止出来たという成功体験を持つことです。
成果に繋がらなければ担当者のモチベーションは下がり、周囲からは不要論も囁かれるでしょう。振動測定からメンテナンスという流れが途絶えてしまえば、やがて故障を体験することになりかねません。
まとめ
運用していくうちに、振動測定によるコンディションモニタリングには、トレンド管理が大切だということが分かってきます。
絶対値判定は便利と考えがちですが、絶対値判定に用いることができる数値は理論などで求められるものではなく、その値を出すためには、可能な限り頻繁なデータ収集を行う必要があるのです。
「絶対的な判定基準があり、これを設定することで異常を的確に発見し、自動診断ソフトで原因と余寿命を教えてもらい、処置することが出来る」振動測定(コンディションモニタリング)をシステムで導入すれば、このようなことができると期待をされる方もいらっしゃるかもしれません。
機械から生じる振動や音といった情報は運転条件や周囲の温度によって、時々刻々と変化しています。従って、ある時点の情報だけで良否が決定できる絶対的な尺度はありません。
また自動診断ソフトはロジックに仮数をおいて実施されているので、当然ながらこの設定によって結果が変わります。機械やソフトに任せれば安心と考えず、サポートツールと捉えて上手く使いこなすことが重要です。